Article 14.
GREEN LOGISTICS
Emisi karbon yang menyumbang cukup banyak terhadap perubahan iklim hingga iklim ekstrim sudah banyak dibicarakan dan menjadi prioritas utama dunia di dalam mengatasinya. Perubahan iklim yang signifikan menyebabkan selain ruang udara menjadi kurang baik untuk kehidupan, juga menjadi penyebab menurunnya produktivitas hasil pertanian yang diperlukan sebagai ketersediaan pangan dunia. Dan sektor logistik turut menyumbang emisi karbon ini dalam jumlah yang signifikan yang membuat laju pemanasan global bertambah cepat (iklim berubah). Logistik yang dimaksud mencakup kegiatan pengiriman (transportasi) dan penyimpanan (storage). Data dunia mencatat emisi karbon global naik 5-7% setiap tahunnya (25% nya dari transportasi pengangkut barang (logistik).
Green logistics adalah pendekatan untuk meminimalkan semua dampak negative terhadap lingkungan dari aktivitas bisnis logistik, terutama jejak karbon. Ini artinya seluruh kegiatan dalam rantai pasok dan penyimpanan serta pengkemasan di sektor logistik harus minim dari emisi karbon, tidak merusak lingkungan dan mengadopsi prinsip keberlanjutan.
Menyikapi pertumbuhan logistik, khususnya logistik berpendingin untuk pengiriman dan penyimpanan produk yang peka akan perubahan temperature karena sifat kimia, phisik dan mikrobiologi nya, tekonologi tepat guna di dalam pengadaan infrastrukturnya menjadi perhatian utama. Istilah cold chain logistics menjadi pemberitaan utama tentang pangan global karena perubahan iklim yang begitu cepat dengan cuaca ekstrimnya.
Apa saja yang menjadi focus penanganan logistik rantai dingin yang merentang dari first mile ke last mile, atau rantai pasokan dengan penyimpanan dan pengiriman akhir ke konsumen, meliputi:
1. Green Harvesting
2. Green Production
3. Green Processing
4. Green Distribution
5. Green Shipment
6. Green Storage
Proses greening (hijau – ramah lingkungan) yang berhubungan dengan makanan, minuman, farmasi, dan jenis produk lainnya yang peka temperature, memerlukan bahan pendingin (refrigerant) yang bukan hanya ramah lingkungan, tetapi juga harus berkelanjutan, dan pasokan sumber energi menjadi syarat utama. Pemakaian seperti panel surya, passive refrigerant, dan lainnya akan sangat membantu di dalam menjaga energi berkelanjutan yang menjadi syarat utama. Jenis active refrigerant ramah lingkungan seperti freon dengan Global Warming Potential (GWP) rendah, ammonia, CO2, dan golongan Hydro-Carbon, akan membantu menjaga lingkungan serta efisiensi pemakaian energi.
Apa manfaat penerapan green logistics dalam kegiatan di bisnis logistik, sebagai berikut:
1. Efisiensi biaya
2. Reputasi dan Citra bisnis
3. Kepatuhan regulasi
4. Inovasi dan Diferensiasi Produk
5. Pengurangan resiko pasokan
6. Efisiensi stok dan persediaan
7. Akses ke pasar baru
8. Efisiensi sumber daya
9. Kemitraan yang berkelanjutan
Montreal Protocol ataupun Kigali Protocol telah membuat peraturan didalam penerapan logistik berpendingin, baik untuk ruangan dingin domestik dan komersial untuk penyimpanan dan pengiriman produk peka temperature, juga untuk ruangan dingin tempat tinggal penduduk. Semua berfokus pada penggunaan bahan pendingin (refrigerant) yang tidak merusak lapisan ozon ataupun menimbulkan efek rumah kaca.
GRREN LOGISTICS
Carbon emissions, which contribute quite a lot to climate change and extreme climates, have been widely discussed and are the world’s top priority in overcoming them. Significant climate change causes air space to become less good for life and also causes a decrease in the productivity of agricultural products which are needed to provide world food. And the logistics sector also contributes to carbon emissions in significant amounts which makes the rate of global warming accelerate (climate changes). The logistics in question include shipping and storage activities. World data records that global carbon emissions increase by 5-7% every year (25% of which is from goods transport (logistics).
Green logistics is an approach to minimizing all negative impacts on the environment from logistics business activities, especially the carbon footprint. This means that all activities in the supply chain and storage and packaging in the logistics sector must have minimal carbon emissions, not damage the environment and adopt sustainability principles.
1. Green Harvesting
2. Green Production
3. Green Processing
4. Green Distribution
5. Green Shipment
6. Green Storage
The greening (green – environmentally friendly) process related to food, beverages, pharmaceuticals and other types of temperature sensitive products requires refrigerants that are not only environmentally friendly, but must also be sustainable, and the supply of energy sources is the main requirement. Uses such as solar panels, passive refrigerants, and others will be very helpful in maintaining sustainable energy which is the main requirement. Types of environmentally friendly active refrigerants such as freon with low Global Warming Potential (GWP), ammonia, CO2, and the Hydro-Carbon group, will help protect the environment and efficiently use energy.
What are the benefits of implementing green logistics in activities in the logistics business, as follows:
1. Cost efficiency
2. Reputation and business image
3. Regulatory compliance
4. Product Innovation and Differentiation
5. Reduction of supply risk
6. Stock and inventory efficiency
7. Access to new markets
8. Resource efficiency
9. Sustainable partnership The Montreal Protocol or Kigali Protocol has made regulations in the application of refrigerated logistics, both for domestic and commercial cold rooms for storage and delivery of temperature sensitive products, as well as for cold rooms where residents live. All focus on using refrigerants that do not damage the ozone layer or cause a greenhouse effect.
Article 13.
APA TREN RANTAI DINGIN MENDATANG DI TAHUN 2024
Oleh Silvia La Wajah.
Rantai pasokan global berada di bawah tekanan yang belum pernah terjadi sebelumnya selama beberapa tahun terakhir, namun logistik rantai dingin selalu berbeda dan memiliki margin yang baik, terutama jika dibandingkan dengan logistik kontrak atau kargo kering.
Volume pasar, seperti dilansir Grand View Research dalam Laporan Analisis Pasar mereka, pasar makanan beku global (dalam laporan ini mencakup buah-buahan & sayuran, kentang, daging, makanan siap saji, ikan/makanan laut) “diperkirakan akan meningkat pada tingkat pertumbuhan tahunan gabungan (CAGR) sebesar 5,2% dari tahun 2022 hingga 2030”. Hal ini akan memberikan tekanan pada keseluruhan arus transportasi rantai dingin, khususnya untuk penyimpanan dingin di kota-kota yang padat penduduknya. Komoditas yang digunakan dalam penyimpanan, seperti baja dan kayu, saat inimahal dan sulit ditemukan karena masalah rantai pasokan, akan terus menantang pembaruan fasilitas penyimpanan pendingin yang ada dan perlu diperbarui, serta kapasitas untuk membangun yang baru.
- Visibilitas: Wawasan kualitas yang lebih tinggi sangat menentukan bagi produk-produk berpendingin, oleh karena itu pada tahun 2024 akan ada lebih banyak investasi pada perangkat lunak yang dapat meningkatkan visibilitas di seluruh rantai pasokan . Peralatan yang lebih baik perlu tersedia untuk secara efektif memantau kargo yang sensitif terhadap suhu dan menciptakan rantai dingin yang tidak terputus yang memiliki visibilitas real-time mengenai kondisi produk (sebelum, selama, dan setelah peti kemas) menggunakan data yang tidak terputus. Pemantauan real-time akan menjadi lebih tepat, dengan perangkat berkemampuan GPS ditempatkan di dalam kontainer. Kecerdasan buatan juga akan diuji untuk menyesuaikan efisiensi tenaga kerja, membantu prediksi , dan mendukung manajemen inventaris penyimpanan dingin untuk memastikan efisiensi dan keamanan. Terakhir, visibilitas juga akan meningkatkan kemampuan penelusuran pangan, yang merupakan fitur yang sangat diminta oleh konsumen di seluruh dunia.
- Farmasi baru dan pertumbuhan kelas menengah: Dengan berlangsungnya globalisasi, peningkatan populasi lansia, dan masalah kesehatan terkait dengan usia lanjut, akan mempengaruhi pertumbuhan industri farmasi, sehingga memberikan dorongan dalam investasi dan inovasi. “Dengan banyaknya permintaan terhadap obat-obatan inovatif dan produk-produk biofarmasi, serta pertumbuhan penjualan produk-produk yang sudah ada, pertumbuhan ini juga akan dipengaruhi oleh meningkatnya kelas menengah global yang memiliki pendapatan rumah tangga yang lebih tinggi” kata Ahmet Sayli, Head of Product Growth , Maersk Logistik Rantai Dingin. Bahkan jika pertumbuhan ekonomi diperkirakan akan melambat pada tahun depan, di beberapa negara berkembang, munculnya “tren makanan sehat” dan peningkatan permintaan suplemen probiotik seperti kombucha, protein premium, atau produk berbasis kafein, diperkirakan akan tumbuh dan mendorong pertumbuhan ekonomi. logistik yang diperlukan untuk memindahkannya.
- Otomatisasi: Tahun depan, otomatisasi akan menjadi kata kunci untuk logistik rantai dingin. Perusahaan akan berinvestasi lebih banyak dalam upaya mengoptimalkan proses dan alur mereka, mengoptimalkan penggunaan data , dan meningkatkan skalabilitas solusi tersebut. Hal ini sebagian disebabkan oleh cepatnya penuaan angkatan kerja, dan daya saing pasar akibat diciptakannya teknologi baru. Elemen otomatisasi dan solusi robotik akan membantu memerangi kekurangan tenaga kerja khususnya dalam penyimpanan dingin, meningkatkan efisiensi dan mengurangi limbah.
- Keberlanjutan: Industri rantai dingin membutuhkan banyak energi. Kebutuhan akan transisi yang kuat sudah jelas, khususnya dalam penggunaan energi terbarukan untuk pembangkit listrik di lokasi (misalnya tenaga surya) dan untuk proses tambahan. Gerakan yang dimulai dari perusahaan FMCG yang menggunakan transportasi rantai dingin ini akan semakin relevan pada tahun 2024 karena perusahaan yang bergerak di bidang rantai dingin akan menuntut tindakan nyata dari penyedia logistiknya. Masalah terkait lainnya yang akan kita lihat adalah tantangan terkait dengan penuaan infrastruktur. Pembaruan yang diperlukan pada gudang rantai dingin, fasilitas, dan lain-lain untuk memenuhi persyaratan efisiensi di pasar akan menyebabkan penghapusan infrastruktur yang tidak efisien dan tidak patuh energi secara bertahap di seluruh dunia. Mulai dari bahan pendingin yang berkelanjutan, hingga infrastruktur yang lebih baru , serta tuntutan akan strategi keberlanjutan yang solid , tahun depan akan menjadi tahun yang penting bagi para pelaku rantai dingin untuk menunjukkan komitmen mereka dan menjalankan kebijakan transisi energi mereka.
- Investasi dingin pada makanan segar: Di tahun-tahun mendatang, kita akan mengamati lebih banyak bisnis dan penyedia rantai dingin yang berinvestasi dalam pengemasan dan penyimpanan makanan segar, mengembangkan fasilitas untuk kegiatan ini, agar tetap mendekati tahap akhir.
- Integrasi yang lebih kuat: Saat ini, perusahaan-perusahaan produsen makanan bermitra dengan penyedia rantai pasokan yang sepenuhnya terintegrasi , yang dapat membantu mereka di seluruh rantai pasokan mereka. “Tren ini tidak akan berhenti dalam waktu dekat. Pasar rantai dingin akan terus mencari lebih banyak integrasi untuk logistik mereka, untuk menambah nilai serta meminimalkan serah terima dan pemborosan dalam rantai dingin mereka” kata Hans Kroes, Pemilik Produk Bisnis Global dari Cold Chain Logistics di Maersk. Pada tahun depan, aliansi dan kemitraan yang lebih strategis antar pemain akan dibentuk untuk meningkatkan efisiensi, mendapatkan visibilitas yang lebih baik, dan membangun aliran cerdas yang juga dapat meningkatkan keberlanjutan.
Suku bunga yang tinggi, inflasi, dan permintaan konsumen yang lebih rendah berdampak pada investasi infrastruktur rantai dingin. Meskipun terdapat hambatan yang kuat , wilayah tertentu di dunia akan mengalami pertumbuhan pada tahun-tahun mendatang.Menurut laporan terbaru oleh Precedence Research, pasar logistik rantai dingin “bernilai sebesar USD 304,8 miliar pada tahun 2022 dan diperkirakan akan melampaui sekitar USD 892,6 miliar pada tahun 2030” dan “diperkirakan akan tumbuh pada tingkat pertumbuhan tahunan gabungan (CAGR) sebesar 14,7% selama periode perkiraan tahun 2023 hingga 2030”. Peningkatan ini juga akan bergantung pada pertumbuhan industri farmasi dan layanan grosir online (jaringan supermarket meningkatkan penawaran online merekaDantoko gelap), serta peningkatan pengiriman dari petani langsung ke konsumen tanpa perantara. Secara keseluruhan, pasar akan melihat peningkatan fokus pada digitalisasi untuk mendorong visibilitas dan otomatisasi, persyaratan keberlanjutan yang lebih kuat, pertumbuhan kelas menengah yang siap untuk mengubah permintaan, investasi pada produk segar, dan semua ini sambil menghadapi perekonomian global yang penuh tantangan. Oleh karena itu, produsen yang menggunakan logistik rantai dingin perlu mempersiapkan, menguji, dan merencanakan logistik mereka dengan bantuan penyedia logistik terintegrasi yang baik.
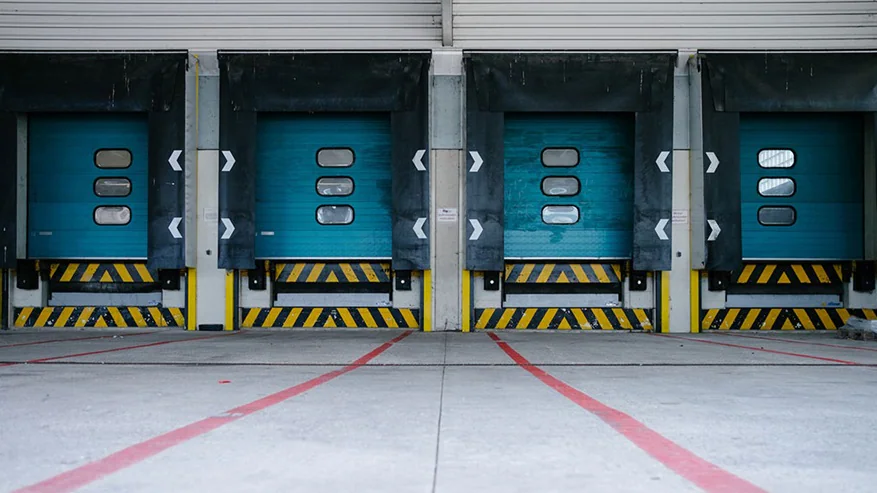
Article 12. 5 (five) Essential Planning Steps For A Successful Steps Warehouse Label and Sign Installation
Demand for warehousing space is at an all-time high, driven in large part by a boom in retail e-commerce sales. If you’re in the process of planning a new warehouse or distribution center or expanding your current facility, there are a several key preparation steps to keep in mind to ensure that your warehouse labels and signs meet your needs and your go-live date.
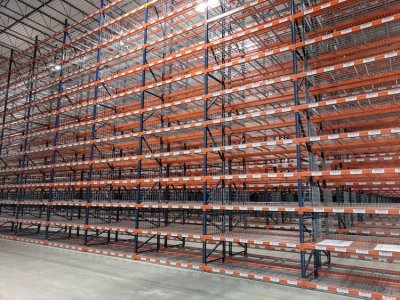
Make sure your racking and facility are ready for labeling, including clean racks and clear aisles.
1. Include Your Label Manufacturer on the Project Planning Team.
Don’t wait too long to plan for your barcode location labels and signs. Poor preparation might lead to errors, rush production charges or delays in your go-live date. Include ID Label on your project team to manage all the aspects of label and sign preparation and installation. This allows you to focus on other critical project components.
Racks and beams should be clean and ready to be labeled. Dirt and dust can quickly accumulate during storage and installation, which can significantly diminish a label’s adhesive values.
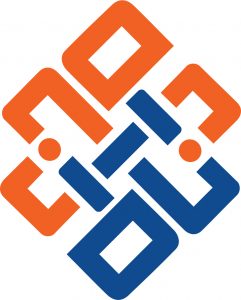
2. Order the Right Barcode Labels and Signs for Your Environment and Technology.
Be sure to consult with your label manufacturer to address the following considerations:
a. What scanning technology will be used?
b. From what distance will your labels be scanned?
c. What kinds of surfaces will the labels be applied to?
d. Will the labels be used in cold or freezer environments?
e. Do your rack labels need to accommodate wire-deck hangover?
f. Will you run an up or down picking operation?
g. Will you use vertical location rack labels?
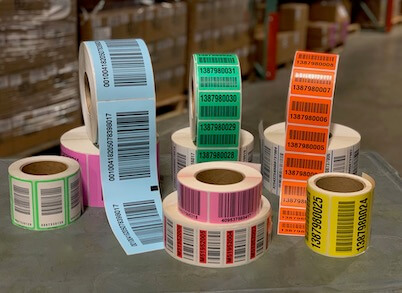
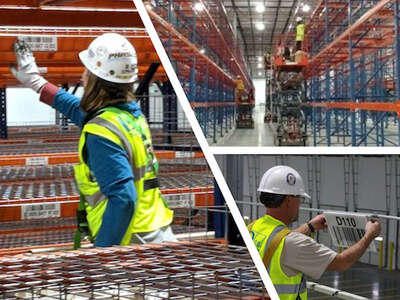
3. Identify Bulk Storage Locations and Signage Needs.
Analyze your floor plan and layout to determine how many bulk storage locations there are and how you will identify those areas. Professional warehouse line striping will ensure that your bulk storage space is organized for maximum efficiency and management.
ID Label typically recommends using long-range scanners and overhead retro-reflective hanging signs with barcode images. They come in a wide variety of designs and materials, including angled and double-sided. PVC signs are sturdy and tend to work well in typical warehouse environments where open dock doors can increase air flow.
Durable floor plate kits are another option to consider, especially when long-range scanning is not an option.
Include ID Label on your project team to manage all the aspects of label and sign preparation and installation. This allows you to focus on other critical project components:
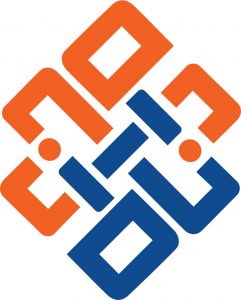
4. Make Sure Your Racking and Facility Are Ready for Labeling.
Clean Racks – Racks and beams should be clean and ready to be labeled. Dirt and dust can quickly accumulate during storage and installation, which can significantly diminish a label’s adhesive values.
Equipment Access – Understand what type of equipment can fit in the aisles to reach upper-level racks.
Power Availability – Active electrical receptacles should be available to power lifts and booms. If not, portable generators will need to be rented.
Facility Access – Confirm what time of day personnel or installation vendors have access to the facility. If access is limited to evenings or weekends, this can impact installation staffing requirements and costs.
5. Order Preprinted LPN Labels in Advance.
LPN labels will be a vital part of your new facility to efficiently identify pallets, cases, cartons, totes and other moveable units.
Preprinted LPNs are typically less costly than labels printed in-house. They also meet the needs of today’s automated smart warehouses that demand greater efficiency, speed and productivity. Set up your preprinted LPN labels in conjunction with the implementation of your WMS system to ensure you hit the ground running on day one.
ID Label offers a “Make-and-Hold” quarterly inventory program that helps lower costs even further while also providing same-day shipping on your next quantity of sequential LPNs.
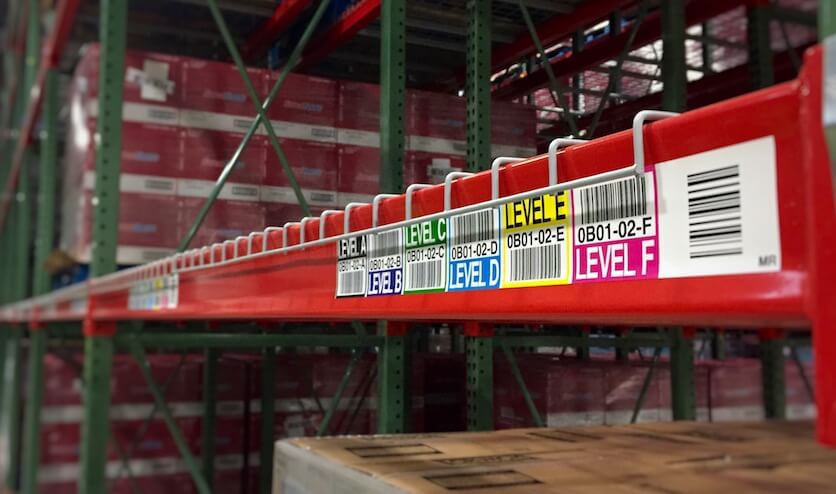
Article 11.
HOW IOT CAN HELP RETAILERS SUCCEED IN A POST-PANDEMIC WORLD
By: Ajay Rane, SCB Contributor
After months of having storefronts shuttered, retailers across the country will spend the coming weeks reopening their spaces for the return of business. But as they do, they need to ensure they’re providing safe environments for employees and customers alike — a feat that’s easier said than done due to the coronavirus contagion.
From warehouses to brick-and-mortar setups, retailers must reconsider their operational models to enable proper social distancing and sanitation, while still prioritizing customer experience.
Internet of things (IoT) devices can support retailers as they navigate these changed circumstances. When deployed across retail operations, such devices can mitigate the amount of manual intervention needed to maintain product integrity and service shoppers. Here are some of the ways the IoT can help retailers adjust to a new world of business, and adhere to critical safety standards.
1. Remote Warehouse Management.
To ensure the security and integrity of retail inventory, warehouses require regular monitoring, an activity that historically has been completed manually by facility employees. This process has entailed physically checking and adjusting room or container conditions, such as humidity or positioning, to accommodate product sensitivities.
Under new social distancing and sanitation guidelines, retailers need to find ways to limit unnecessary foot traffic that can contribute to the spread of disease, while still protecting their products. IoT sensors attached to containers can support warehouse management in these efforts, by collecting and transmitting data on inventory conditions to remote retail staff. With this technology, warehouse managers can monitor the temperature and pressure of containers from a distance, thereby keeping human contact, and the spread of germs, to a minimum.
Additionally, IoT sensors can help to remotely monitor inventory levels through automated reporting, to ensure that warehouses have enough product to meet changes in customer demand. The sensors can also report location and motion, to prevent theft or tampering of goods.
2. Store Capacity Monitoring.
As part of their plans for reopening brick-and-mortar operations, retailers also need to consider how they’re going to facilitate a safe environment that supports social distancing for employees and customers. With new safety guidelines suggesting that stores limit the number of shoppers allowed inside to 50% or less of their typical occupancy, one such consideration is how retailers will monitor shop capacity.
Posting store “bouncers” at entrance and exit points to count shoppers as they come through is one option, but this method is prone to human error and may jeopardize employee and shopper safety. Instead, retailers can place IoT sensors on shelves or grocery carts to automatically, continuously and accurately count the number of shoppers in store, so they can more reliably adhere to safety regulations.
3. Optimized Shipping.
Despite retailers’ best efforts to foster safe storefronts, some customers might still be hesitant to return to public spaces the moment that stay-at-home advisories lift, preferring instead to continue shopping online. To that end, it’s equally important for retailers to ensure an optimal e-commerce experience, with packages delivered in a safe and timely manner.
To meet these expectations, retailers can attach IoT-enabled devices to shipping containers to secure up-to-date insights into package whereabouts. Data collected by these devices can also help to immediately identify delays caused by warehouse complications or heavy traffic, so that retailers they can quickly reevaluate and optimize shipping routes that will further enhance customer experiences moving forward.
In addition to location, IoT devices can monitor shipping container conditions, such as temperature, humidity, shock and tilt, so that retailers can be confident that their products are being properly cared for across the supply chain. This level of control is especially important for providers of perishable items such as groceries and medicine, for which fluctuations in conditions can not only damage the goods but also pose health risks to receiving customers.
As retailers navigate their reopenings in the aftermath of the coronavirus outbreak, IoT technologies can provide the insights needed to effectively execute adjusted operations. To sustain these devices — especially if warehouses and stores are widespread, or retailers are shipping to great distances — retailers need to have a simple, low-cost network that enables reliable global connectivity. This way, all operations are on the same network with the same devices, allowing retailers to manage their supply chains with ease so that they can focus on more pressing issues, such as providing safe shopping experiences for customers and employees alike. By optimizing the supply chain with IoT devices, retailers can mitigate safety risks while still fulfilling customer product and service demands to satisfaction.
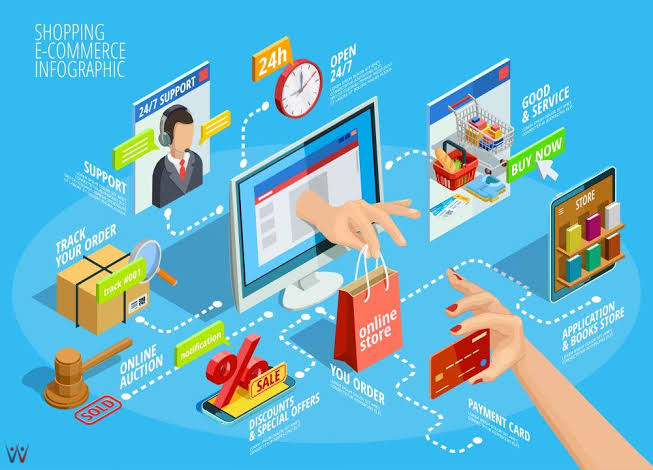
Article 10. HOW DOES COLD STORAGE BENEFIT YOUR BUSINESS
Cold Storage could be an excellent place to store fruits and vegetables. With the ability to prolong life and prevent food spoilage, cold storages deteriorate the microorganism activities. The common advantages of storing food at cold storages include cooling them beyond average temperature. However, their benefits do not limit to only cooling. Let’s look at some of the lesser-known advantages of cold storage for both personal and business use.
- Adjustable temperature.
Cold Storages are often equipped with custom refrigeration system units (a temperature controller) that allow temperature adjustments and flexible monitoring. The custom units delay the food spoilage and dehumidify them. The chill temperature remains at 2°C, while solidified is at – 18 °C, and deep-frozen is at – 29 °C. Then again, a few items are to be stored at room temperature, which might be anywhere in the range of 8°C and 15°C relying upon the prerequisites. - Cooling – made affordable.
Temperature dominancy costs a lot, however, it’s not the same case with cold storages. Customized cold storages come in varied sizes and shapes ensuring relaxed refrigeration of your food. Relaxed room refrigeration can save up your costs while keeping the food spoilage at a minimum. As it keeps the fruits and vegetables refrigerated at the right temperature, cold storages minimize waste and hence, are economic. The benefits of cold storages are maximum when your goods are in bulk. It prevents direct sunlight to come in contact with your goods. - An efficient backup.
Along with providing an additional capacity region, cold storages can likewise be used for extra protection of your products. The contents of the refrigerator can be easily moved to cold storage if you have a chance of a power shortage. The cold storage temperature is consistently constant and allows your stock to stay refrigerated at a constant temperature for a longer period. By using portable storages like Wire racks and Free stands, you can quickly move your products in or out and ensure that they’re surrounded by fresh air. - Less Heat, Lesser Noise.
Having enough space and capacity is a constant challenge no matter how big our room is. The same goes for installing an in-home refrigeration system in a place that can be used for something else. And due to their fans and compressors in action, they end up producing extra heat in the surroundings. Cold Storages can eradicate the problem producing excessive heat. As they’re situated outside the building, they can reduce the heat as well as keep control of the noise issues too.
A cold storage facility comes in once your business begins to develop. A progressively huge business implies greater advantages, including a more extensive client base. It might be ideal if you thought of warehouse storage as a tool that will assist you in developing your business. According to sources, the cold storage industry is expected to see a rise of 13–15% over fiscals 2019–23, mainly driven by rising demand for processed food, fresh fruits & vegetables, seafood, and bio-pharmaceuticals in exports markets. So, if you’re planning to invest in a cold storage business, you can be assured of better returns and profitability in the long-term. (source: gubbagroup.com)
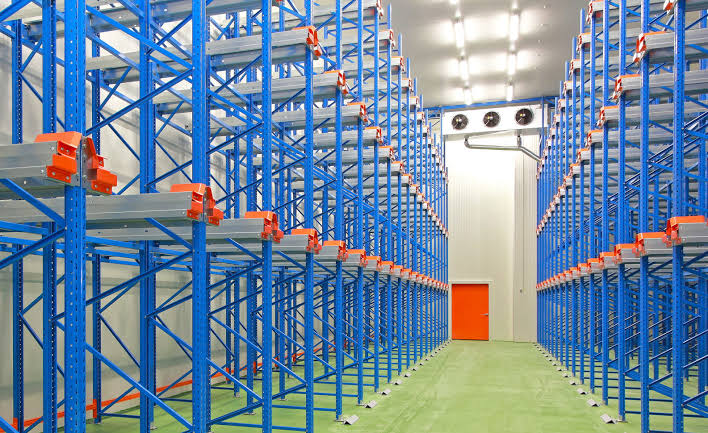
Article 9.
BUILDING an HVAC COMPANY PERSONALITY (One Step at a Time)
Everybody has a personality. Whenever you think of someone you know — your mother, neighbor, coworker, or anyone else — you picture their personality. You can easily imagine how it feels to be around them, their sense of humor, their talkativeness, and a thousand other character traits.
Companies have personalities, too. And whenever people think of your company, they will immediately think of its personality. And that personality — the taste in their mouths as they think of you — will determine if they become repeat customers.
Not every company personality is the same. It shouldn’t be. One company might sell itself as challenging the status quo and constantly pushing boundaries. Another might cultivate an image of tradition and reliability — offering the same tried-and-true products and service that it has for decades.
We know when a company has made us feel that we can trust it. However, shaping your company’s personality requires intentionality and commitment. Here are several specific ways to do it.
1. Customer Service.
Exceptional customer service is the most obvious. Your employees are the face of your company, and as such, they have a profound influence on building its personality. When a customer (or potential customer) interacts with an employee, that will be the most memorable part of their experience. If the employee treats them poorly, they will certainly remember it. Likewise if they were given exceptional treatment by an employee.
Make sure your employees know the importance of everything they do. The way they present themselves, talk to customers, spend their time while at a jobsite — it will all build up your company personality. Take the time to train them on how to interact with everyone (especially more difficult customers) with complete professionalism.
But go beyond the basics, too. Add a gift bag with the purchase of a unit or the signing of a maintenance agreement. If you believe in the work of your technicians or your products, promise refunds if the customer isn’t happy.
2. Social Media and Website.
Social media offers the unique ability to continue building a relationship with the customer, even when not directly involved with them. Your treatment of social media will build your business’ personality. The videos your company shares, the humor you inject in your posts, and more all have the potential to show potential customers who they will be buying from if they choose your company.
And don’t underestimate this power. People want a company they know and can trust to buy from. A prospective customer might learn about you, go onto your business’ social media page, and see a list of posts showcasing your company culture, your technicians, and ways you served your community. That will build a personality and a relationship far better than an extremely outdated social media page.
The same can be said of your website. If a customer goes to your website and finds it difficult to use, they will likely assume that the rest of your company is clunky and hard to work with. But the opposite is also true. If the website is easy to use, streamlined, and a chatbot opens up with helpful, kind suggestions, the website visitor will assume that booking a call and interacting with your technicians will be just as easy. And all of these things build your company’s personality, leading to the formation of relationships with customers.
3. Trucks and Advertising.
Your advertising and your trucks will construct your company identity as well. The moment an old (or new) truck rolls into a customer’s driveway, a message is being sent about the personality and the quality of your company. Similarly, a wrap on your truck — whether it shows a graphic or just the name of your company — will portray whether your business is put together and professional. All of these things lead to the customer building a relationship with your company’s personality and walking into their discussions with your employees with optimism and trust.
Direct advertising is a way for you to speak directly to customers and tell them about your company’s identity. Whether you invest money in a radio ad, television commercial, or direct mail advertising, invest time, money, and thought into deciding exactly what message you want to get across. The right script or text can portray your company as relatable, trusting, caring, yet entirely professional.
by Gordon White (is the web editor for the news, looking for quality content written by HVAC industry proffesionals).
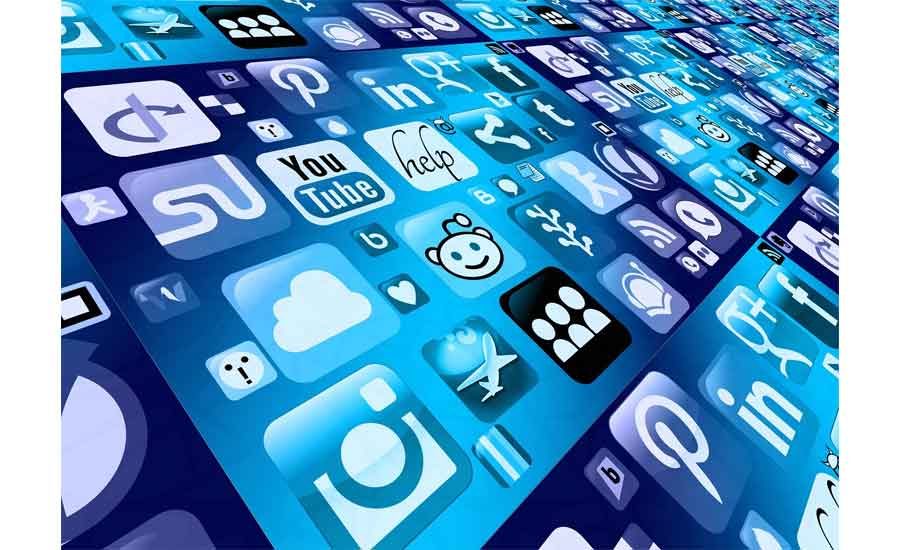
Article 8. FIVE KEYS TO RESTARTING YOUR SUPPLY CHAIN AFTER COVID-19
As supply-chain managers begin working toward a new normal after the COVID-19 crisis, they’ll be trying to understand dynamics they haven’t encountered prior to this pandemic — not the least of which is how their vendors and customers are handling their restart, and how the marketplace is going to rebound. Will demand be recharged, or are we looking at a slow start that grows in momentum more deliberately?
In either case, there will be pressure to think ahead and quickly process those variables, as companies struggle to recalibrate and return to profitability. Planning will require greater precision, and supply-chain managers will need to process data in real time, to align the business with the supply chain. Once demand picks up, businesses will have to be agile enough to respond to a quickly changing environment.
With so many variables to account for, here are five suggested steps for stabilizing supply-chain operations, optimizing throughput, and maximizing profits in the coming weeks as the economy reopens.
1. Get a head start in planning.
First, assess both inbound and outbound supply chains, and understand your inventory and work in process. Do you believe your tracking data is correct, or do you need to conduct a physical inventory? Imagine two weeks after the COVID-19 restart, when you discover pick orders that didn’t get entered or processed in the last week before the shutdown. If you had work in process at shutdown, did it go through the appropriate quality check before the shift ended? Further, don’t consider just the material aspects. Look at the time and cost of international shipments, as they might be different than pre-crisis. Since many pockets of the country are going through the curve at different rates and times, global commodities are likely to see a whiplash effect as stockpiles of raw materials head to new markets.
Also, set aside time to develop an alternative sourcing strategy, and push for 100% transparency in supply-chain tracking. After that strategy is developed, risk-assess it by asking questions, such as what happens if the U.S. and China implement new tariffs? And what financial risks do I have with currency translations?
2. Understand desired talent skills.
Identify the critical skills and roles in your manufacturing process, and consider reassessing those jobs whose functions were redefined by the crisis. Develop a depth chart for these roles, and evaluate the weak points. Next, create a training plan to fill in skills gaps, but also consider augmenting your team with people who have proven expertise that matches your business’s critical needs.
Recruiters should look across industries for skills that align with your new needs and can increase the team’s overall strength. For a start, look at program managers, supply-chain leaders, and support roles. Staff augmentation can be a boost to the bottom line, with direct support or even as a team function with coaching by a seasoned veteran.
3. Connect to the supply chain with increased engagement.
Chances are that pushing for 100% transparency in your supply chain is an immensely challenging task, but you can get there with a plan and by improving your processes. With new stresses and unknowns being faced daily, it makes sense to add methods and tools to gain visibility. Work with your upstream vendors and downstream customers; they’re facing the same changes and challenges as you. Talk to them frequently, and ensure that the entire process works seamlessly toward establishing an achievable schedule, every day for every shift.
4. Put the emphasis on safety.
A successful restart is going to require adapting your production and inventory-management practices for the impacts of social distancing, guards and barriers, as well as sanitizing workspaces, people, tools, inventory and finished goods. Any time you re-engineer a workflow or production space, add safety into every step. We recommend applying a 5S review to operating a facility, while keeping people safe from common injury vulnerabilities and the coronavirus. Also, safety walkthroughs are critical, especially if changes have been made on the plant floor and people are in new roles. Look at new traffic patterns and areas where new work-in-progress stocks are created. Further, consider what will happen to personal protective equipment (PPE) supply and demand as industries restart around the world.
5. Understand investment-tradeoff effects on the supply chain.
Lastly, understand risks of capital debt versus reinvestment. Can your post-COVID-19 supply chain grow to meet this incremental addition of capacity? Throwing in additional production capacity requires diligence in and of itself. Some industries deal with great tools and methods and have detailed playbooks. Some of these could help your team not only meet the challenges of a COVID-19 supply chain, but also grow stronger.
As businesses start planning for the restart, they have only one chance to get it right. Consider these steps to get your business back to normal.
Written by : Bill Currence, managing partner and founder of Cornerstone Consulting Organization (has been edited).
Article 7. FINDING THE RIGHT NATURAL REFRIGERANT SYSTEM FOR INDUSTRIAL REFRIGERATION, by: Michael Garry
“Stakeholders debate whether to use low-charge ammonia, ammonia-CO2, or CO2”
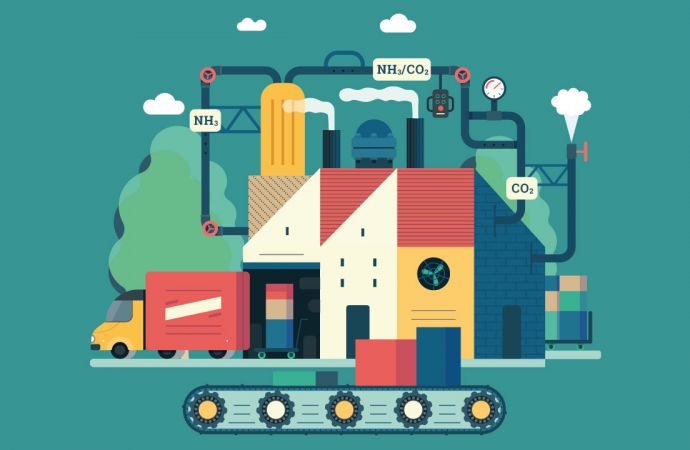
Inexpensive and highly efficient, ammonia (NH3) has for decades dominated the industrial refrigeration landscape. But the refrigerant’s position has evolved in recent years.
For one thing, ammonia’s unavoidable toxicity has led to an industry-wide effort to develop systems that use far less charge than traditional liquid-overfeed systems. This has resulted in the proliferation of low-charge technologies, from central DX and packaged units to systems that combine ammonia and CO2. More recently, transcritical CO2 systems, which have been used predominantly in food retail, have begun to emerge in industrial facilities as an option that removes ammonia altogether.
So now two natural refrigerants, ammonia and CO2, or a combination of both, are competing for space in cold storage and industrial plants. Any of them is superior to synthetic refrigerants like R22 or HFCs, but which of the natural options is best for a given application?
One of the more popular industrial options to emerge in recent years is the NewTon ammonia/CO2 secondary packaged system, produced by Japanese OEM Mayekawa. Mayekawa said last year that it expected to sell 330 sets of NewTons during its current fiscal year, which runs from April 2019 to March 2020. (The number of sets is equal to the number of compressors used; some NewTon units contain more than one compressor.) This would bring the total number of sets sold past 2,000 (95% in Japan) since the system was introduced in 2008.
The first Mayekawa NewTon system in Australia was installed and commissioned last July in a new cold-storage distribution center in Western Sydney; the work was handled by Tri Tech Refrigeration Australia, Sydney, Australia. The project encompassed five NewTons: three medium-temperature NewTon-C units supplying 708kW (201.3TR) of cooling capacity; and two low-temperature NewTon R6000 units providing 198kW (56.3TR) of capacity. The combined cold-storage area is 44,094m3 (1,557,165ft3).
Mack Hajjar, Projects Engineer for Tri Tech, noted last October that “based on energy usage data obtained so far, overall typical compressor power consumption is considerably lower than a conventional two-stage pumped [liquid-overfeed] ammonia plant servicing an industrial cold store of a similar size.”
Hajjar’s energy assessment was challenged by Stefan Jensen, Managing Director, Scantec Refrigeration Technologies, Brisbane, Australia, who designed and constructed what he calls the first stick- built centralized low-charge ammonia system “of the modern era” in 2012-2013, in Perth, Australia. That system proved to be 67% more efficient than a comparable R404A air-cooled system in the same area belonging to the same end user, he said.
In a letter to Accelerate Magazine (January 2020), Jensen cited a paper “Comparing Energy Consumption and Life Cycle Costs of Industrial Size Refrigeration Systems,” authored by T. Lund, M. Skovrup and M. Holst of Danfoss, and presented in August 2019. “In all three jurisdictions investigated (Rome, Frankfurt and Oslo), the R744/R717 (CO2/NH3) cascade system is less energy efficient than the equivalent dual-stage R717 system with liquid overfeed.” For example, the Danfoss study found COPs of 4.35, 4.15 and 3.60 for two-stage liquid-overfeed ammonia systems for the highest loads examined (900kW/256TR low temperature; 2,700kW/768TR medium temperature) in Oslo, Frankfurt and Rome, respectively; by contrast the comparable ammonia/CO2 cascade systems had COPs of 3.92, 3.76 and 3.35.
Jensen’s favorite energy metric is specific energy consumption (SEC) in kWh/m³*a (m³ for refrigerated space, a for annum). He pointed out that according to a paper authored by Mayekawa researchers H. Asano and N. Mugabi, the best SEC achieved by NewTon systems is approximately 35kWh/m³ for a distribution center with a refrigerated volume of 44,000m³(1,553,845ft3). The paper, “Actual Energy Conservations by Using NH3/CO2 Refrigeration System,” was published in the proceedings of the 3rd International Conference of Saving Energy in Refrigeration and Air Conditioning (ICSERA), held in 2013.
Jensen compared the SEC for the NewTon with that of a low-charge DX two-stage ammonia system. According to ICR 2019 paper #466, “Real Energy Efficiency of DX NH3 versus HFC,” authored by Jensen, a centralized DX NH3 system delivers an SEC of 20-24 kWh/m³a when servicing a distribution center with a refrigerated volume of 44,000 m³, compared to the 35kWh/m3a for the same volume cited by the Mayekawa researchers.
Jensen doesn’t believe in ammonia-inventory reduction at all costs. “The art is to reduce the ammonia inventory and at the same time improve energy efficiency compared with a stick-built ammonia liquid overfeed system and transcritical CO2,” he said. “This is an art that isn’t mastered by many, but [ammonia’s] transport and thermodynamic properties make this a task that is nevertheless achievable.”
Energy-efficiency improvement “is the path to long-term survival of the ammonia industry as a whole,” Jensen said. “Nothing will match the energy performance of an ammonia refrigeration system done well. The industry has to start doing these systems well or lose significant market share.”
But he acknowledges that some operators are willing to pay an energy penalty to keep ammonia out of the refrigerated space.
To do an ammonia system well, Jensen said, equipment suppliers need to under- stand “how ammonia behaves during evaporation in tubes and what causes that behavior.” In addition, contractors need to know “what determines the optimum operating envelope for evaporators, and specify the correct design parameters to suppliers.”
Another important design feature needed to maximize energy efficiency in low-charge ammonia refrigeration systems is to minimize or eliminate the presence of liquid in suction lines during all operating conditions. “This is exactly what a centralized, low-charge ammonia system does,” Jensen said.
Jensen pointed to the potential risk asso- ciated with ammonia/CO2 cascade heat exchangers: If the ammonia and CO2 mix, they form ammonium carbamate, which seriously impacts operation. In one case Jensen cited, a system was shut down for four months, and repair costs were half the original cost of the system. In the U.S., “insurance costs for NH3/CO2 cascade are escalating and driving users towards centralized low-charge ammonia.”
Supporting Energy Claims for NewTon
Tri Tech’s Hajjar agrees that a two-stage DX ammonia system is, in principle, more efficient than its ammonia/CO2 cascade counterpart.
Ammonia DX systems have a number of advantages, Hajjar noted, including no liquid-ammonia pumping requirement, high-efficiency, speed-controlled reciprocating compressors, no high- or low-side heat exchangers, no wet-return losses, no suction superheat and no (or less) hot-gas relief load if defrost drainers are used.
An end user who uses reticulated subcritical CO2 and/or water-cooled condensing with cooling towers, like a NewTon system, is “deliberately sacrificing energy efficiency for increased safety and in some cases [reduced] cost,” said Hajjar. “In our [NewTon] application, the question was not whether to use a secondary refrigerant, but which one and how – DX or pumped ammonia were definitely out of the question.”
He stands by his previous comments that the NewTon’s energy consumption is considerably lower than that of a conventional two- stage pumped-ammonia liquid-overfeed system when comparing similar-size facilities.
But that estimate was low because in spring/summer the power consump- tion would be higher, he acknowledged. “Realistically, power consumption would be closer to 1.5GWh p.a.” This translates to 34.09kWh/m3a for a 44,000m3 (1,553,845ft3). facility, which is consistent with what Mayekawa researchers Mugabi and Asano predicted – 35 kWh/ m3a for NewTon in a 44,000m3 space.
By contrast, if a site like the one in Australia with the first NewTon units were to instead use conventional two-stage pumped ammonia, “I would expect energy usage of 3GWh (68kWh/m3a),” said Hajjar. He referred to figure 8 in Jensen’s paper, “Real energy efficiency of DX NH3 versus HFC,” where “the bulk of conventional two-stage pumped ammonia systems consume 40-70 kWh/m3a.”
Hajjar also noted that SEC, as a performance metric, “doesn’t normalize for proportion of low-temperature/medium-temperature, door usage, geographic location, facility layout, etc. Realistically it is more of a general guide for efficiency comparisons.”
It should also be noted, said Haggar, that the NewTon ammonia system is not a conventional cascade system, because it uses CO2 as a secondary fluid only. “It relies on a more efficient ammonia vapor-compression cycle for refrigeration, instead of compressing and reticulating CO2 in a vapor-compression cycle on the low stage.”
“So while the NewTon NH3/CO2 secondary system sacrifices COP due to their hot- and cold-side heat exchangers, done principally to make the plant safer, there are many features that compensate for this, making the NewTon system very efficient, nonetheless,” continued Hajjar. “As a result, it is important to consider the configuration of ammonia/CO2 cascades when making comparisons, and so the COP comparisons made in the Danfoss study, for example, may not always apply.”
The NewTon’s other energy-enhancing-features, he said, are as follows:
The medium- temperature and low-temperature NewTon systems are independent. Therefore the effective medium-temperature suction pressure and low- temperature interstage pressures are independent, and can be therefore optimized for each respec- tive system. By contrast, in a two-stage system, the medium-temperature suction and low-temperature interstage must be common, and under certain circum- stances not optimized for either stage, or optimized for one stage but not the other.The medium-temperature system uses a single-stage economized cycle. The low-temperature system uses a two-stage cycle with both its respective high- and low-stage cycles economized. This is inherently more efficient than a single-stage medium-temperature cycle providing intercooling for a single-stage low-temperature cycle.The NewTon system does not use hot-gas defrost. A conventional pumped ammonia system uses hot-gas defrost, which relieves a considerable amount of hot gas to suction, thereby increasing energy consumption; with some even relieving to the low-temperature stage, making the system less efficient. It is possible to use defrost drainers to mitigate hot-gas relief loads and return only liquid to the medium-temperature vessel, but “conventional” pumped-ammonia systems don’t always do this.The NewTons have permanent magnet motors, which are high-efficiency motors.NewTon systems don’t have a tendency to draw air and moisture in at negative pressures like conventional low-tempera- ture ammonia open-drive compressor systems, because NewTons don’t have shaft seals. Over time, energy penalties due to trapped non-condensables and water accumulation, which appear in conventional ammonia systems, may not manifest themselves in NewTon plants.
CO2 vs Low-charge ammonia
While some operators are reducing ammonia charge in low- charge or ammonia/CO2 systems, a growing number of industrial facilities are opting for a “no-charge” ammonia system, that is, transcritical CO2. According to Terry Chapp, Principal, Collaborative Solutions, Terry Chapp & Associates, CO2 systems are better suited for industrial systems with smaller capacity – from 50TR (176kW) to 300TR (1,055kW) – than ammonia systems, which can cover up to 2,500TR (8,792kW). Jensen acknowl- edged that for smaller warehouses – under 5,000 -10,000m3 (176,573 – 353,147ft³) in refrigerated volume – the additional cost of a centralized low-charge ammonia system compared to a transcritical CO2 system would require “too long a return on investment.”
CO2 systems are still regarded as working better in relatively cooler climates, though optimized systems have improved efficiencies in warmer climates.
One CO2 operator in the U.S. is Henningsen Cold Storage, based in Hillsboro, Oregon (U.S), which, in June 2018, installed its first transcritical CO2 system – one of the first industrial transcritical systems in the U.S. – at an 111.000ft2 (10,312m²) facility in Grandview, Washington (U.S.). It supplies 187TR (658kW) of refrigeration capacity, 157 (552) for a freezer and 30 (106) for a dock area.
Henningsen, which runs 12 cold-storage warehouses, mostly in the Pacific Northwest part of the U.S., is one of the most efficient operators in the North American refrigerated warehouse industry. Its facilities, including ammonia and CO2 systems, average 0.569 kWh/ ft3a (20.3kWh/m³a), compared to an industry average of 1.13 (40.4). (Henningsen is measuring the energy consumption of the entire facility, not just the refrigerated space.) Under the direction of Pete Lepschat, director of engineering, Henningsen has built several low-charge central ammonia systems that use substantially less ammonia than the company’s traditional plant.
In contrast to Jensen’s DX ammonia systems, Henningsen uses a “minimalist overfeed model,” which Lepschat believes saves more money. At the company’s first warehouse in Salem, Oregon, built in 2013-2014, he installed Evapco evaporator coils with a 1.2-1 overfeed ratio (for every 1.2 part of liquid ammonia, one part evaporates), compared to the 3-1 ratio at a traditional Henningsen facility.
Another technique Henningsen employs to cut ammonia charge is to use what Lepschat calls a “pump-down system” in lieu of a high-pressure receiver. The system features a small vessel that maintains a low-level of ammonia and is continuously feeding the gas to a low-pressure receiver via a subcooler.
In its second low-charge warehouse in Salem, built in 2017, Henningsen was able to reduce SEC to 0.288kWh/ ft³a (10.3kWh/m³a), the lowest in the company, and one of the lowest in the cold-storage industry. This became the standard for all future facilities, including the first CO2warehouse in Grandview. (Henningsen converted another warehouse, in Scranton, Pennsylvania (U.S.), to transcritical CO2 in 2018.)
The installed cost of the Grandview CO2 system was $534,000 less than the Salem ammonia system; between $200,000 and $400,000 was saved by not building a machine room, which also cut 5-6 weeks in installation time. The reliability of the CO2 system and low- charge-ammonia standard has been the same. But on an energy basis, the Grandview CO2 system, which uses an adiabatic gas cooler, had much higher energy costs than the standard facility’s system, though that was before several energy-efficiency measures were added. Those included: dock dehumidification, evaporator/condenser fan control, hot-gas defrost, gas cooler optimization, compressor VFDs and a glycol pump VFD. In the subsequent commissioning of the system, the low-temperature suction setpoint was changed from -25°F (-32°C) to -16°F (-27°C). In addition, evaporator and gas cooler fan speeds were changed from fixed to modulating.
In Lepschat’s most recent data, which covered January 2019 through January 2020, the Grandview CO2 system has an SEC of 0.384kWh/ft3yr (13.7kWh/m³a), well below the average for Henningsen’s facilities (which is itself considerably below the industry average) but still 25% above the standard Salem number. But Henningsen is working with system manufacturer Carnot Refrigeration to improve rack efficiency, Lepschat noted. In addition, he aims to improve his fan control systems. With those changes, “I think we will either match Salem [on energy consumption] or actually do better.”
In other areas, the CO2 system is saving Henningsen money compared to the standard low-charge ammonia plant in Salem. For example, the CO2 system uses far less water in its adiabatic gas cooler, which also reduces the sewer bill, and it requires no water treatment. In addition, an ammonia facility requires a full-time engineer to keep an eye on it, while a CO2 plant does not. Maintenance on the CO2 system takes place just twice annually, and generally involves minor upgrades “like changing the oil on your car,” said Lepschat. And a CO2 facility can dispense with U.S. federal regulatory updates for PSM (process safety management) and RMP (risk management plan) that are needed at an ammonia warehouse; Lepschat estimates he saved “six figures” at the CO2 facility by not having to develop an initial PSM/RMP plan.
In the event that energy parity with Salem ‘s standard is approached or matched, the savings on other factors would result in operating costs at the Grandview facility that are up to 20% better than Salem’s, said Lepschat.
Another factor favoring transcritical CO2 is heat recovery. “CO2 has a pretty big advantage in this area,” said Lepschat. This is because the sensible and latent portions of the discharge gas are almost the inverse of those for NH3, that is, 70% of the rejected heat is sensible and 30% latent for CO2, as opposed to 30% sensible & 70% latent for NH3, he explained. That means a CO2 system is better for generating hot water and space heating than an ammonia system.
At the Grandview facility, heat reclaim is used to warm the floor under the freezer and to minimize defrost in the freezer by getting rid of moisture in the dock area. The system defrosts with hot gas.
Another consideration is the number of compressors used. At Grandview, Henningsen employs 15 semi-hermetic reciprocating compressors in its CO2 system. “So if one goes down, we have 14 to back it up,” Lepschat said, and replacement costs are not high. “Redundancy is built in.” By contrast, an ammonia system may use one large screw compressor, with one expensive replacement unit.
Jensen said that some CO2 systems may have better annualized energy performance than large-scale centralized ammonia systems with liquid overfeed because these CO2 systems employ multiple small reciprocating compressors and have very little or no liquid in the suction lines.
Given everything he knows now, Lepschat was asked which refrigerant he would lean toward for future plants, ammonia or CO2? “I never say never, but as of today I see no advantage to building an ammonia refrigerated facility.”
The article originally appeared in the March 2020 issue of Accelerate Magazine.
Article 6.
SUPPLY CHAIN RISK MANAGEMENT IS BACK
The world is getting riskier – and the most advanced supply chain leaders are getting smarter about risk. Is your supply chain risk – ready?
As we know, more global companies questioning how to assess and manage these risk and prepare their supply chains accordingly. Which precautionary measures make sense, and how much do they differ by industry? With conducted research by interviewing supply chain managers across Europe to understand how they assess risks, what they do prepare, and how they respond to disruptions.
Risk On The Rise
Natural disasters are particularly dramatic illustrations of the difficulties facing supply chain managers. Even in a comparatively begin year, suc as 2019, global losses due to earthquakes, floods, fires and the like reached US$ 150 billion. But dramatic spikes are happening more often, with nearly US$ 350 billion in losses recorded in 2017. These high costs, in combination with long recovery times, have triggered many companies to reassess their supply chain strategies and footprints to make them more resilient to any kind of disruption (figure 1), from Mc Kinsey & Company.
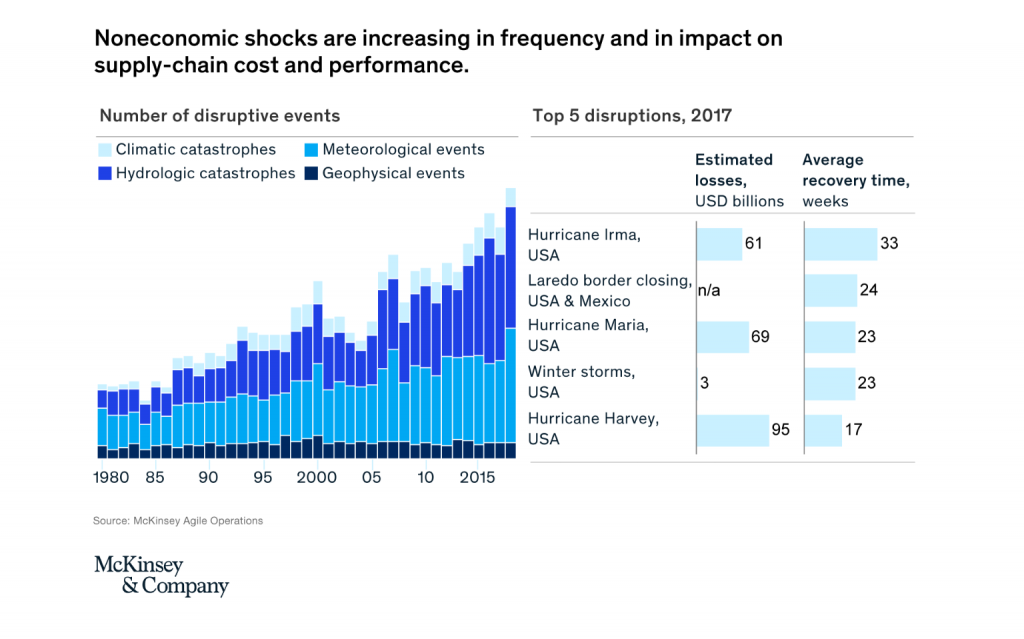
How Advanced Companies Manage Supply Chain Risk
The degree of professionalization of supply chain risk management varies widely. Many companies still follow a more-reactive approach in responding to supply chain disruptions. That said, almost all the companies that surveyed diversify their operations and implement multi – sourcing strategies wherever feasible and economically justifiable. Working closely together with their suppliers and performing regular supplier audit is part of their general business practice. On an ongoing basis, they monitor the most relevant risks – such as regulatory changes or changing customer demand. But relatively few invest much time and money in automating any of these activities. When hit by sudden supply chain disruptions, they build temporary task forces to manage the issue on an ad hoc basis. In some cases, precious line is lost due to insufficient preparedness. By developing and assessing scenarios with different probabilities for pre-identified risks, the most advanced organizations can make high – level impact calculations that enabled better prioritization. Accordingly, prioritization is based not only on financial factors, but also on business specific factors, such as regulatory and strategic considerations and the company’s specific risk appetite. Supply chain risk leaders develop set of reactive and proactive response strategies, and foster general risk awareness among their employees by creating an openness to address potential shortages and failures.
Creating Supply Chain Resilience
In sight of increasing business complexity and growing overall uncertainty, establishing a systematic supply chain risk management approach becomes more and more relevant. Many companies relying mostly on reactive measures today want to improve their supply chain risk management capabilities – and say they are willing to invest more time and resources to do so.
Digital Supply Chain Transformation with a Human Face
Increasing supply chain resilience is a leading theme for many globally operating companlies with complex operations. Based on the experience, to suggest a four step that can be tailored to a company’s needs based on its individual starting position. Less – advanced companies will typically start by concentrating on establishing an end-to-end process first and their more-advanced counterparts may instead focus more attention on advancing steps 3 and 4.
- Identify the most relevant events and risk threatening to disrupt the company’s supply chain operations.
- Define possible outcome scenario and assess their high level impact. Depending on the level of exposure and magnitude of the impact, the company prioritizes risk for targeted attention.
- Develop response strategies for prioritize risks. It is essential to create an unbiased process to decide where to invest and how to prepare. A systematic calculation of business cases is the foundation for these investment decisions. The trade-off between investing in prevention versus taking the risk of being hit when unprepared – resulting in severe disruptions and losses needs to be quantified. Different dimensions important to the company need to be incorporated to create a meaningful business case, otherwise it is difficult to get the required funding for risk management.
- Finally, supply chain risk management needs to be incorporated into regular decision-making and planning processes. Embedding risk-management capabilities as a regular ingredient of business decisions in operations is the first step towards creating a true risk culture and a resilient company.
A systematic classification of risks and development of a related response strategy, is essential to improve supply chain resilience strategically – while keeping required investment to a minimum. A simple framework can help by classifying risks on two axes: the vertical estimates to what extent a risk can be anticipated, while the horizontal quantifies the risk expected impact (figure 2), from Mc Kinsey & Company.
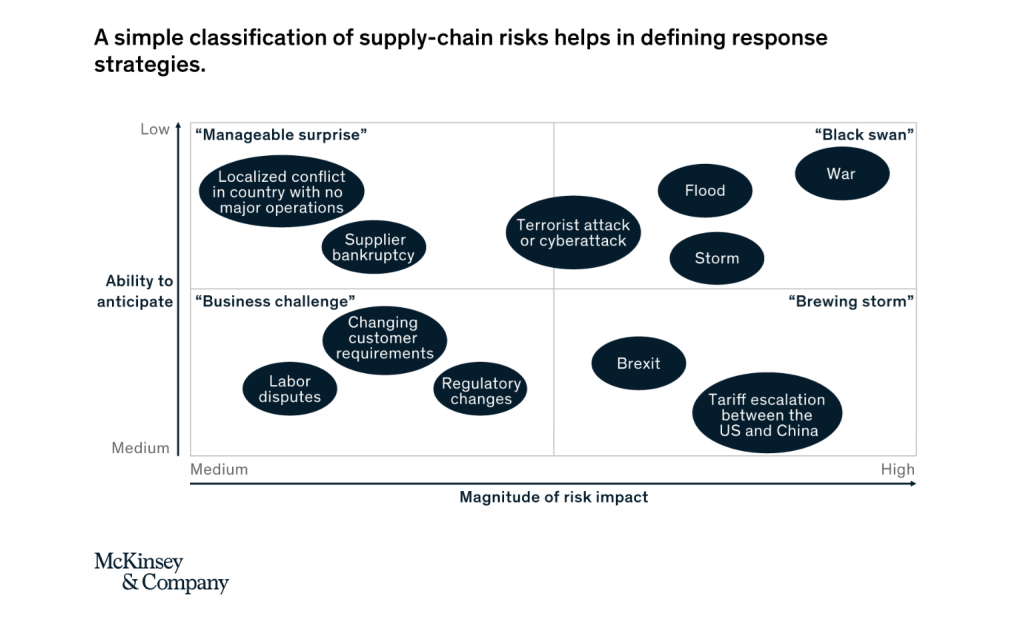
Low-impact risks that are hard to anticipate, such as the bankruptcy of an individual supplier or a localized conflict in the country without major operations can be accepted or avoided to a certain extent by diversifying operations. Systematically implementing a dual-sourcing strategy, through nominating new suppliers or negotiating a second source of supply from the same supplier, help mitigate this risk category.
High-impact risks that are hard anticipate, including natural disasters, terrorist attacks, or cyber attacks, can be managed by building strong crisis management capabilities and resilience throughout the system. A supply chain risk management team can introduce a systemic risk monitoring process which can be enhanced by regular scenario planning exercises. Through keeping healthy reserves for parts with long recovery times, companies can prevent some supply chain disruptions. Another way to mitigate risks which are difficult to anticipate is transferring risk to other parties. Taking out insurance and introducing risk-related contact language are possible answers.
Low-impact risk that are relatively easy to anticipate, such as labor disputes, regulatory changes, or changes in customer preference (for minimal plastic usage or increased product sustainability, for example), can be managed proactively by increasing the robustness of the supply chain system. The most important single measure, though, is solid training of the workforce to handle everyday risk. Encouraging employees for voice concerns about possible defects and disruptions helps create a general risk awareness as a first step to managing disruptions. IT systems and tools can then help to continuously monitor disruptive trends and events.
High-impact risks that are relatively easy to anticipate, including Brexit, US-China trade regulations or de-carbonization targets, need the most attention. A systematic review of the supply chain setup may be advisable. Possible response strategies include redefining the sourcing strategy by, say, raising the share of local suppliers or revisiting the manufacturing footprint by moving some manufacturing operations out of certain areas. Establishing CKD operations in countries with high import taxes on finished products can be another option. The review of the inventory build-up strategy helps optimized service level by increasing safety-stock levels for critical components which can’t be sourced from alternative locations. In some cases, preparing for changes in demand can be appropriate answer.
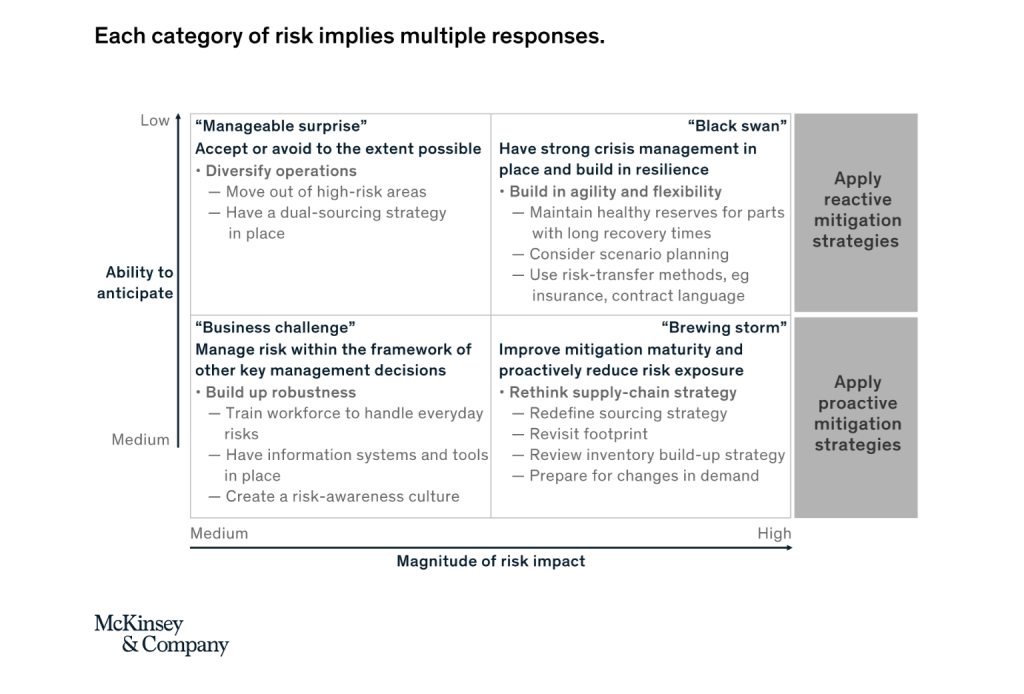
Article 5.
HOW DIGITALIZATION OF THE SUPPLY CHAIN WILL REDUCE GLOBAL FOOD WASTE
From GCCA Book Directory – by Leuven, Belgium – The scale of the global food waste problem is staggering. According to reports, 1.6 billion tons of food are lost or wasted every year, equating to a total value of $1.2 trillion being wiped from the supply chain. With one-third of the total amount of food produced globally being misused, the industry needs to look towards innovation and digitalization to combat this ever-growing trend.
Through embracing technology and digitalizing the food supply chain, a move can be made towards reducing the amount of food waste and loss within the industry. Not only that, but it can also help ensure there’s enough resource to sustainably support the future global population.
With the UN’s Sustainable Development Goals setting a target of halving food loss and waste by 2030, I’ve looked at how the digitalization of the supply chain could help decrease global food waste.
The need for innovation to reduce waste
Although food waste is evident across the entire supply chain, the vast majority comes at the very beginning (during production) and at the very end (during consumption). The former of these is more common within developing countries, where the infrastructure is of a poor standard and cannot handle the food thus creating waste, whilst the latter is more pronounced in developed countries with waste being caused by both retailers and consumers.
According to the Boston Consultancy Group (BCG), the amount of food waste createdin the supply chain is set to rise 1.9 per cent from 2015 to 2030. You may think this is a small rise, but when put into
perspective with the current 1.6 billion tons wasted every year, this figure will increase by 30.4 million tons.
To combat this increase in waste, the food supply chain needs to go under a digital transformation. From production and processing to the retailers themselves, systematic changes are required in food supply chain management to help everyone utilize this precious resource more efficiently and cut back on the amount of waste we’re creating as a society.
Utilizing IoT in the supply chain
Through having better levels of communication across the supply chain, the amount of food waste produced can be reduced. Each aspect of the supply chain must be in constant contact with one another to ensure our resources are managed efficiently.
This is where the Internet of Things (IoT) can support and improve supply chain efficiencies. Based on having interconnected and interrelated systems and processes, IoT allows each aspects of the food industry to have access to key data around the supply, production and management of produce, which can help reduce the amount of waste created. Without the wider adoption of IoT in the food supply chain, the levels of food waste could increase by 50-90 per cent as a result of several combined factors, such as the increase in food demand due to the ever-growing population.
By allowing all stakeholders within the supply chain access to key data shared across integrated systems, processes can be optimized further along in the chain to maximize how the produce is handled. For example, a bad batch of apples with a high percentage of internal browning would require a specific equipment set up and would need to be fine-tuned to ensure the maximum value can be extracted from the apples. It is believed having this connectivity could save the supply chain up to $60bn in waste.
Through having this pre-warning of any information regarding a batch of produce, farmers can not only optimize their yields by reducing the risk of waste, but the other stakeholders can also plan accordingly to try and prevent the cause of waste.
Having this ability to share data through IoT can also help reduce waste from a consumer standpoint. Retailers could use the real-time data in stores to showcase when the produce was harvested or picked and offer insights into the projected “sell by date”. This can educate consumers further on how long they have to eat the produce, thus helping reduce food waste through the implementation of technology.
Using innovation to improve current infrastructure
As well as utilizing IoT, the supply chain can also use digitalization to help improve the infrastructure it currently has in place.
Cold chain plays a huge role in the food industry creating waste, mainly due to poor infrastructure – in India, for example, $14bn is lost every year through poor cold chain facilities. However, implementing innovative and efficient systems can go a long way in addressing the food waste issue – particularly in developing markets. By deploying more advanced cold chain solutions within the emerging markets, which share the data across the supply chain through IoT, it could prevent large-scale food loss and waste.
The conditions can also change in cold storage, and temperature affects many sorting technologies, so the ability to link cold storage sensors to packing equipment can enhance performance.
But this is nonexistent in many emerging markets, creating poor food storage and transportation conditions early in the value chain that lead to large-scale food loss. Deploying more-advanced supply chain solutions—including cold chain in developing markets—could reduce the problem by $150 billion annually.
Investing in efficient sorting and grading systems is a key approach in helping the supply chain reduce the food waste created earlier in the supply chain.
We want to know everything about the produce. Everything from the weight and size through to the external properties and defects, and even the internal chemical composition to predict ripeness and longevity. But there are only two points when you can gather information on individual pieces of fruit: when it’s picked and when it is sorted. These are the critical data acquisition points.
KPIs need to be based around understanding the types of defect types and classes/grades per batch, to help create a complete map and total view of the produce. This, in turn can help build up big data, meaning every batch gives you new insights and allows you build a bigger picture, creating the ability to make even more informed data-driven decisions. Where appropriate, data can be shared and augmented to ‘context’, such as weather data or geo-tagging.
The final step is to layer artificial intelligence to start to understand previously unseen patters and even more efficient ways of working.
Although these KPIs tend not to be designed to help limit the amount of waste produce, utilizing sorting and grading technology can automatically support a waste sensitive environment by recovering any produce and reusing it for another purpose, such as cattle feed or pet food. This means that rather than creating food waste, an alternative, more suitable use is found. Lower quality fruits can be used for juices or pulped to become products such as guacamole or apple source, whilst starches can be used for medical purposes. All of these help us reduce waste and put the lower quality produce to better use.
Going digital to fight food waste
With the ever-rising stats around food waste, now is the time for the industry to adopt a more digitalized approach across the supply chain. Implementing integrated and innovative systems will allow all key stakeholders, from field to fork, to efficiently manage food and reduce the risk of waste at loss.
Digitalization won’t just help from asustainability aspect, but also help businesses drive their own profitability by improving processes and efficiencies. It becomes the answer to the push-pull paradox for commercial benefit and combating global food waste.
At TOMRA, we’re committed to creating sensor-based sorting and grading systems to help the supply chain win the battle against food waste. Through our systems, we aim to help food businesses maximize yields and ensure any produce can be recovered and reused, increase productivity with high capacity sorting and provide consistent high-quality food assurance.
We also understood that we must take the next steps. TOMRA Insight is our answer to connect our sorting and grading systems, extract valuable information on the sorting performance and the produce, and make it transparent to the food businesses. Incorporating this further into a digitalized supply chain will help to close the link from farm to fork in the future.
Article 4.
INNOVATIONS AND ADAPTATIONS IN THE COLD CHAIN,
By Nils Markmann
The rise of targeted therapies and the globalization of specialty pharmaceutical commercialization present a host of opportunities for manufacturers. The foundational premise is clear: More commercial and clinical trial drugs are being shipped to more patients in more countries than ever before. Healthcare is becoming more innovative and more accessible at the same time.
With these opportunities, however, come great challenges. The increase of global clinical trials for high-value cold chain products means that the stakes—and the costs—for each trial have risen dramatically. The distribution of specialty medications to emerging markets means that the total supply chain must be evaluated more stringently. The industry now operates in an environment where there is no “acceptable loss” of product or samples. As a result, global manufacturers must constantly evaluate the advances in technology, processes, and resources that keep cold chain products safe. They must remain vigilant over the growing and diverse risks in the supply chain and understand the need for increased expertise from their partners. They must stay focused on continuous improvement across all parts of their supply chain to ensure that drugs are delivered safely and effectively, while risks are mitigated appropriately.
Here, we explore three macro-trends in the global pharmaceutical supply chain—specifically the temperature-controlled supply chain—and key takeaways that manufacturers should consider as they work to drive new growth globally.
Targeted therapies and unique temperature needs
Pharmaceutical manufacturers have seen a significant shift in their development goals and processes. The pursuit of the next blockbuster, small-molecule product has given way to excitement around new, targeted therapies, biologics, and personalized medicines—all of which are driving demand for better temperature control in the supply chain.
Increasingly, there is a need for more than just cold shipping. Instead, there is an expanded need for a highly connected and functional supply chain. In fact, “cold chain” no longer accurately describes the full suite of solutions that manufacturers need. The industry is moving toward “temperature control” as the all-encompassing term, in recognition of the wider range of new temperature requirements for biologic products. From samples and biologics shipped at “body temperature” (close to 37 °C) to controlled room temperature (about 20–25 °C), all the way down to ultra-frozen products stored at -80 °C, the new spectrum of temperature needs makes it clear that the traditional cold chain (a range of 2–8 °C) is no longer sufficient to accommodate all product needs.
New temperature requirements necessitate new packaging solutions. It’s difficult to maintain product temperatures in a laboratory or storage setting, and the difficulty increases exponentially when products must travel at a consistent temperature across thousands of miles over the course of hours or days. The right packaging is essential to ensuring product integrity.
Fortunately, the options for packaging and monitoring technologies have expanded significantly in recent years. Semi-active packaging, including expanded polystyrene (EPS) and expanded polyurethane (EPU) systems, is still common and is often is the more economical choice for local, short-distance transports. Semi-active solutions are unable to regulate their own internal temperatures and require different packaging configurations seasonally, even within the same route. For this reason, semi-active packaging is best suited for controlled, short-haul routes. Many semi-active solutions are only intended for use a single time and must be discarded afterward, causing them to be somewhat of an environmental liability.
New options are focused on offering longer durations of temperature control with lighter materials that have a smaller environmental impact. Passive packaging solutions are more technologically advanced and provide proven temperature control over long distances. These solutions rely on specific engineering to create a highly stable interior storage environment. Independent testing indicates these solutions perform five to seven times more efficiently than semi-active solutions. Phase-change material (PCM), comprised of paraffin or salt-based solutions, allow for more precise temperature control to maintain product stability over long distances or through extreme climates. Many packaging manufacturers are now developing their own vacuum-insulated panel (VIP) containers, combined with PCM solutions, for easier handling and storage.
On the monitoring side, GPS technologies and tracking equipment that include automatic start-up and shutdown mechanisms (so they can be used safely on flights) offer a real-time view into a shipment’s status and data-driven peace of mind throughout a product’s entire journey.
Although monitoring technology can be a benefit, it can also be a disadvantage for some products. Manufacturers should partner with organizations that can help them find the solutions that align with their product-specific needs. Selecting too much technology (e.g., using a container with an electric-powered refrigeration system when a PCM-based solution would work), can create unnecessary expense. Selecting not enough protection can risk the integrity of a product.
Global clinical trials and expanding market presence
In tandem with the shift in the types of drugs being created, there’s also a shift in where drugs are being developed. It is estimated that pharmaceutical sales in Brazil, Russia, India, and China will grow to nearly a quarter of a trillion dollars by 2016 (1). There are more than 186,000 registered clinical trials taking place across the globe, and global pharma’s volume has more than doubled over the last decade (2).
New patient populations are needed to test the latest in pharmaceutical advances. Increasingly, regulatory bodies mandate tests need to be conducted within the specific countries in which manufacturers seek approval to launch and market a product. As a result, the importance of efficient, global clinical trials will increase dramatically in the coming years.
As the global market for clinical trials expands, there are significant hurdles that manufacturers must clear to ensure products arrive at the right place, at the right temperature, at the right time. Manufacturers and logistics partners often must navigate geopolitical roadblocks to maintain a high-performing clinical and commercial supply chain. Apart from global concerns in hot-button countries, manufacturers must consider all local, regulatory landscapes in which they do business. They must evaluate the existing capabilities in the market and disruptions in the supply chain to determine how all of these factors may impact shipping time.
Improper customs paperwork, for example, can delay or compromise even the most optimally packed shipments. Delayed flights, weather issues, or airport personnel strikes can cause product transport issues that could delay or even derail entire clinical studies. Manufacturers can avert these issues by deploying knowledgeable, trained logistics personnel within their global markets. Placed at varying locations around the world and operating within a proven infrastructure, these experts should be able to mobilize local knowledge and expertise on a real-time basis—substantially reducing risk of temperature excursions.
Global expansion may be the goal, but global support has to come along with expansion. When conducting clinical trials in emerging markets with time- and temperature-sensitive medications, manufacturers should consider working with specialty logistics experts in each specific country. Local, in-market knowledge of regulations and transport infrastructure can mean the difference between keeping the clinical supply chain moving and grinding a productive trial to a halt.
Focus on risk mitigation
The financial risks of mishandled shipments are fairly clear for commercial drugs that must remain temperature-controlled: lost sales and revenue, lost productivity, and lost opportunity to improve patient lives. The risks are no less severe on the clinical side, where transportation failures involving clinical product or patient samples could result in studies being compromised. Delays and other disruptions in trials impact the expected time to market for a product, potentially putting millions or billions of future revenue dollars at risk.
As a first step, it is crucial for manufacturers to identify the needs for all of their shipped products, especially those of high value. Meeting risk mitigation and quality objectives within the framework of an effective cost/performance strategy can be a simple matter of combining the right packaging fit with the right service fit for each individual application.
Beyond that, though, global manufacturers are also challenged with needing to understand worldwide political issues and infrastructure limitations that may impact logistics.
Take the following situations as examples:
Cambodia’s Phnom Penh International Airport has no freezer available and only one refrigerator set to one range that is neither qualified nor controlled. In conjunction with technological restrictions, clearing customs can take many days. It may be possible for logistics partners to refresh refrigerants, but there are no guarantees.In Laos, the rainy season lasts from August to September. With limited airport facilities, products can be left on the runway. Manufacturers can avoid unnecessary damage by sending products before or after the rainy season.With the growing population and spend on healthcare in Latin America, it’s an ideal location for a growth plan, but each country within the region has different regulations and resources.
Although conducting trials and commercializing in new markets represents opportunities to expand needed therapies to new patients, it also represents millions of dollars worth of risk when working with cold-chain products. Proactive planning—combined with a knowledgeable logistics partner that can help navigate global nuances—will help protect products, ensure that temperature controls are met, and increase effective use for patients.
A solution for every therapy
Manufacturers worldwide are investing more in their supply chains. A $15-billion increase in spending for global biopharmaceutical logistics is expected between 2012 and 2018 (3). As global predictive growth explodes, shippers and trial sponsors can expect an increase in regulatory and overall logistics complexities that foster in-market resources across the globe. The spend on cold chain logistics was more than $8 billion worldwide in 2014 and is expected to exceed $10 million by 2018 (3).
The rise of targeted therapies and solutions for rare diseases has created even more challenges for manufacturers, as the demand for personalized, high-value drugs with more active pharmaceutical ingredients (APIs), shorter shelf-lives, and strict temperature requirements increases. As products become more targeted, so will the logistics solutions. This trend indicates pharmaceutical companies are (or will become) more invested in supply chain operations.
Fortunately, sophisticated logistics providers are investing in new technologies and improving their capabilities in order to ensure they can successfully handle the most innovative new products on a global basis. As the supply chain continues to expand in complexity, the relationships between manufacturers and their logistics partners must also grow.
Article 3.
WHY DO YOU NEED A TRANSPORT MANAGEMENT SYSTEM?
A Transport Management System/Software (TMS) is a logistics platform that allows users to manage and optimize the daily operations of their transportation fleets. It comes under the subset of Supply Chain Management (SCM). Its primary function is to plan and execute the physical movement of goods
A Transportation Management System is also an essential weapon in any company’s arsenal. To keep up with the ever-changing business environment, a TMS is a necessity!
The right TMS can optimize your core operations and transform the way your business functions.
Here’s 10 reasons WHY:
A. IMPROVED CASH FLOW
A good transportation management software will help a business immensely in reducing shipping costs.
B. INTEGRATED PLANNING AND EXECUTION
The new generation transport management systems integrate smoothly with existing systems that are essential for managing the transport needs of a company
C. MINIMAL PAPERWORK
Automation of all accounts using a TMS will save precious time and money spent on bulky paperwork.
D. INVENTORY MANAGEMENT
Through TMS, businesses can monitor the lifecycle of orders and shipments in real-time and get status updates on each.
E. SUPPLY CHAIN VISIBILITY
Having this full operational visibility and access to real-time data from all systems is a huge plus. It enables managers to quickly act on any opportunities or resolve any issues that may arise.
F. OPTIMIZED ROUTING THROUGH POOL DISTRIBUTION
Order cycles have shortened and shipment sizes have shrunk. As a result, routing is more critical than ever.
G. TRACKING DRIVERS EN-ROUTE
Driver tracking enables users to assess the optimality of different routes taken by the drivers, which can help to generate a more efficient schedule.
H. ACCURATE ORDER FULFILLMENT
With a reliable transport management system ensures that shipping becomes more accurate.
I. IMPROVING CUSTOMER EXPERIENCE
TMS will bridge the gap between order management and warehouse management systems. It will help to consolidate all customer orders to find the best carrier at the lowest possible price. A win-win for both consumers and businesses!
J. REPEAT BUSINESS AND REFERRALS
The right TMS saves your time and money. It enhances your company’s overall productivity and efficiency.
Article 2.
FIVE IoT APPLICATIONS IN LOGISTICS & SUPPLY CHAIN MANAGEMENT, Written by Brian Ray,
Whether you’re in manufacturing, retail, distribution, or shipping, planning and managing the flow of raw materials and finished goods through your supply chain is a challenge. Materials are often improperly shipped or stored, which can damage sensitive goods. Plus, the sheer size and capacity of a large operation can lead to disorganization in a manufacturing warehouse or distribution facility.
One of the best ways to decrease material waste and improve logistics is with the use of real-time location systems (RTLS
In the past, supply chain tracking and monitoring solutions—like ultra wide-band (UWB) and infrared technologies—required significant infrastructure, which came with a major installation headache and a significant price tag (often $10 per square meter). Today, there are asset-tracking solutions on the market, like AirFinder, that can be installed and operated for 10 times less than UWB and infrared.
Before we get into more details as to what you should look for when selecting a supply chain management IoT solution, let’s look at several use cases of IoT applications in logistics.
Location Tracking
1. Track deliveries from the vendor to the manufacturing facility.
If you work with numerous U.S. vendors to create a single component for your device—say, a network of sheet metal vendors for an auto manufacturer—RTLS can be used to track pallets of this component from every vendor, from the time the pallets are packed until the time they enter your manufacturing yard. This way you’ll know well ahead of time if a shipment is delayed, allowing you to keep production running smoothly with your “Plan B.
2. Track deliveries and materials around your manufacturing facility.
Truck drivers have little to no incentive to ensure your goods are delivered precisely where you’ve instructed, which often leads to lost or misplaced shipments. If you use RTLS, you’ll know precisely where pallets have been placed.
3. Track deliveries and materials inside your manufacturing facility.
Materials moved inside a facility for assembly or shipping often fall prey to what we call the “flat spot problem”— e.g. being left on any flat surface available. Misplaced materials can lead to slower production times, employee frustration, and, ultimately, customer dissatisfaction. With RTLS you know the location of tagged materials, like a specialty test fixture, at all times.
Environment Sensing
4. Monitor sensitive goods to avoid damage or loss.
Some factories regularly receive shipments of perishable or sensitive goods that only stay fresh for a short time, and/or require specific environmental conditions to maintain quality.
Using an IoT application for logistics, you can tag a crate of eggs or a barrel of milk and monitor the humidity in the storage area, the temperature of the product, and the shock and vibration levels these items experience during shipment. You can use this information to notify truck drivers of damaged shipments long before they arrive at your factory, and get a new shipment on its way.
Fleet Management
5. Monitor assets to mitigate risk.
If you’re involved in the transport of goods from point A to point B, you need to know where your vehicles are at all times for safety and compliance reasons. Without a tracking system, it can become easy to make erroneous assumptions. For example, you might assume that Bob is with his assigned vehicle—but what if he took a different vehicle that day? Or what if that vehicle is in the shop and he’s in another, and you’re simple unaware? This type of tracking system allows you to ensure you know where each vehicle in your fleet is so you can hold up your end of the supply chain.
SIX QUESTIONS To Ask Before Selecting An IoT Application For Logistics & Supply Chain Management
- What level of accuracy does the system allow for?
Do you need room-level accuracy, or more specific location capabilities? This will make a difference in the kind of system you select. For some systems (like AirFinder), a higher number of reference points can be added to increase location accuracy.
2. How much infrastructure is required?
If you’re building new construction, systems like infrared or WiFi-based RTLS may work well for you. But if you’re retrofitting a system in your current building, you’ll want to select RTLS that is easier to install.
3. What is the total cost of ownership?
The total cost of ownership is one of the most important considerations for manufacturers looking to implement an IoT-based monitoring and tracking solution. Battery life, tag cost, power consumption, and employee training all come into play when calculating cost, so evaluate them all when considering a solution.
4. How much does each tag cost?
Tag cost varies dramatically. Passive RFID tags can be pennies on the dollar, Bluetooth low energy (BLE) tags can be obtained for less than $15, and WiFi tags are typically around $40-$60. The tag cost, of course, makes an impact on whether or not an IoT-based logistics solution will work for you or not.
5. How long is the battery life for each tag?
Battery life impacts affordability and maintenance. AirFinder tags, for instance, do not beacon continually, so they last up to three times as long as traditional BLE tags.
6. Is the system secure?
When you implement an IoT application of any sort on your network, keeping your data secure is a top priority. The AirFinder system uses multiple layers of device and data security to ensure your data and IT networks are safe. BLE data is encrypted end-to-end using modern AES TLS data transport methods. A “stand-alone” data network, which can be connected via cellular, eliminates IT network vulnerability.
Article 1.
COLD CHAIN MARKET
HOW TO MOVE YOUR BUSINESS INTO THE NEXT DECADE
Over the next five years the cold chain market is expected to grow at a compound annual growth rate of 11%, boosted by the expansion of international trade and the introduction of innovative new operating models that are being employed across many industries, from supermarkets through to the pharmaceutical industry.
As an essential piece of the supply chain puzzle, cold chain involves the storage and transportation of temperature sensitive or perishable products. Having the right tools for the job in these often-harsh environments can be the difference between a successful business and an unsuccessful one, due to the need to be as efficient as possible to avoid wastage or spoilage.
Closer to home growth will come from exploiting the market on the doorstep, by reinventing what the consumer already knows and repackaging it for the modern way of living. The campaign is geared at changing perception, not only about how convenient and healthy frozen foods can be, but also how friendly it is to the average consumer’s food bill, given the reduction it makes to waste.
Overseas expansion will be the big opportunity as the buoyant market is pushed by demand from developing nations such as India and China. With such a rising demand for specific temperature controls relating to food and healthcare products, it’s clear that now is the time to reassess your business and pinpoint where productivity gains can be made to capitalise on the increased demand.
THE EVOLUTION OF MOBILE DATA CAPTURE TECHNOLOGY
In a cold storage environment, making productivity gains, creating more efficient operations and managing costs can all be addressed by a thorough review of the data capture technology in use.
The bottom line is that the effectiveness and reliability of a mobile device will fall along with the temperature, unless a device is specifically designed for the conditions it is expected to perform in.
The list of problems that mobile devices must face in a cold storage environment is long, and can include: LCD screen fogging up, batteries struggling to cope with the cold, frost obscuring screens, frost covering a barcode scanner’s optical port, reduction in drop rating/IP, reduced display refresh rates and ice on the keyboard.
When a device is frequently taken in and out of cold areas, the temperature can affect almost all of its components. However, the end result is the same – reduced user productivity and if you are not careful employee engagement drops too.
The good news is that over the last five years there has been an abundance of investment in technology research and innovation – today’s modern devices have been enhanced to maintain efficiency in temperature-controlled environments like never before.
The changes can often be simple, such as adding big buttons to rugged handheld terminals that can be felt when using thick gloves, through to more complex improvements, such as internal heat sources and seals designed to prevent condensation and battery draining due to the cold temperature. These innovations are now commonplace and can make a huge difference to cold chain operations.
It’s also vital to consider your operational model today and where you think it will be in three or five years time when planning any investment in new devices. If you want to gain a bigger slice of the cold chain market, then you have to be prepared to grow with it. As well as the technical features of the devices, think of the practical implications too. Will the warehouse grow and if so will your people do more miles moving around the warehouse, and will they carry the device or will it need to be mounted to a vehicle? How will the devices cope with wear and tear, especially as demand increases? How will they cope with rapid temperature change if they are taken into different environments? The technology exists to manage these scenarios, but the trick is to determine the fewest variations in order to optimize the investment.
There may also be an operating system issue that needs to be addressed, depending on your current situation. Will software automatically update so that you have the latest version, how can you ensure all of your employees are using the same version? Do you want to use a system that your employees are already familiar with? How will this impact training? Integrating new technology into a fully functioning, and in many cases an increasingly busy, cold store environment is a challenge. But making the right decisions for your business can pave the way for a successful future.
A logistics expert who understands your business challenges and can help you refine and establish your operational and strategic objectives and make the right choices regarding the devices needed. They can also help with deployment and with any training that may be needed to work with specialist devices.
MOBILE TECHNOLOGY ON THE ROAD
As well as ensuring operations run smoothly inside the warehouse, it’s outside on the road where many new technologies can help to optimise a cold chain business.
All too often businesses falter when the pressure is on, and the link that usually breaks first is the one between the warehouse and the lorry. In a cold store environment, mistakes made while loading a vehicle can put standards at risk and slow down the whole operation. When dealing with goods that must be kept at a certain temperature to preserve them, or for hygiene and safety reasons, there can be no weak link or the whole operation will fall down.
With online grocery expected to double to £1.1 billion by 2018, fuelled by the rise of click and collect services, it’s clear that success will depend on slick stock management and tight turnaround times.
Devices used in vehicles and lifts will also be susceptible to similar problems faced in the warehouse. Although similar solutions are also available, it’s another link in the chain that needs to be understood and dealt with properly if gains in productivity are to be made.
THE MANAGEMENT SYSTEM
To cope with the expansion expected over the next five years, cold storage operators will need to consider the demands on infrastructure and how their warehouse management system can support the mobile devices available.
As demand increases, along with the pressure on maintaining temperature, a system that offers a real-time view of inventory and orders can allow warehouse managers to be confident in the ability of their business to deliver – and feel assured when taking on new contracts to grow their business.
Giving employees the tools to do their job, backed up by a solid warehouse management system, will not only boost productivity and efficiency but can also work wonders for morale too.
At an early stage, those involved in cold chain should map out the technology they require to capitalise on the expected growth – and create a roadmap to make it happen. It’s easy to think it will be complex to change technology, and indeed it can be if you are replacing outmoded technology, but with the support of a logistics expert it can be a smooth process. A good logistics partner will look at the situation as a whole and design a solution that can be phased-in according to businesses readiness, finances and capability
THE INGREDIENTS FOR SUCCESS
Any logistics company involved in cold chain will inevitably look at the expected growth in the industry and consider the changes it needs to make to take a slice of the market. The truth is that many more issues will apply to each individual business than can be listed here. Ultimately, it comes down to one central theme – what is the opportunity and what will it mean for our bottom line if we do nothing, something or change completely?
Answering this will drive the change that’s needed and open up further opportunities in the market – or even the opportunity to serve existing customers in a more efficient manner.
Identifying how much ‘stretch’ there is in the existing model is one of the first tasks that should be completed. By mapping out your ambition, and then by doing a gap analysis of what you need compared to what you have, you’ll be able to establish the right path to go down.
You’ll also be able to assess the cost versus the opportunity and the roll out plan – a phased implementation that uses a combination of existing technology and new technology, or a complete replacement. The assessment should also help you see where you’ll achieve the biggest gains and how you should prioritise your implementation.
It is vital the strategy is well planned out. This can be an enormous undertaking so it’s very worthwhile to work closely with a technology specialist, who can help assess the gap you need to close today and help you anticipate the future.
A good partner will use this gap analysis to guide a logistics business to the solution that can maximise the opportunities the market presents today and leave the door open for managing the new opportunities that developments in technology are likely to bring about.
Cold storage and logistics is a dynamic industry and the potential for growth is great. A strategy underpinned by technology is the best way to exploit it and turn opportunity into profit.
Source: Bizibl Group Limited, Registered in England 09091156, 26 Bridge Road East, Welwyn Garden City, Hertfordshire, AL7 1HL